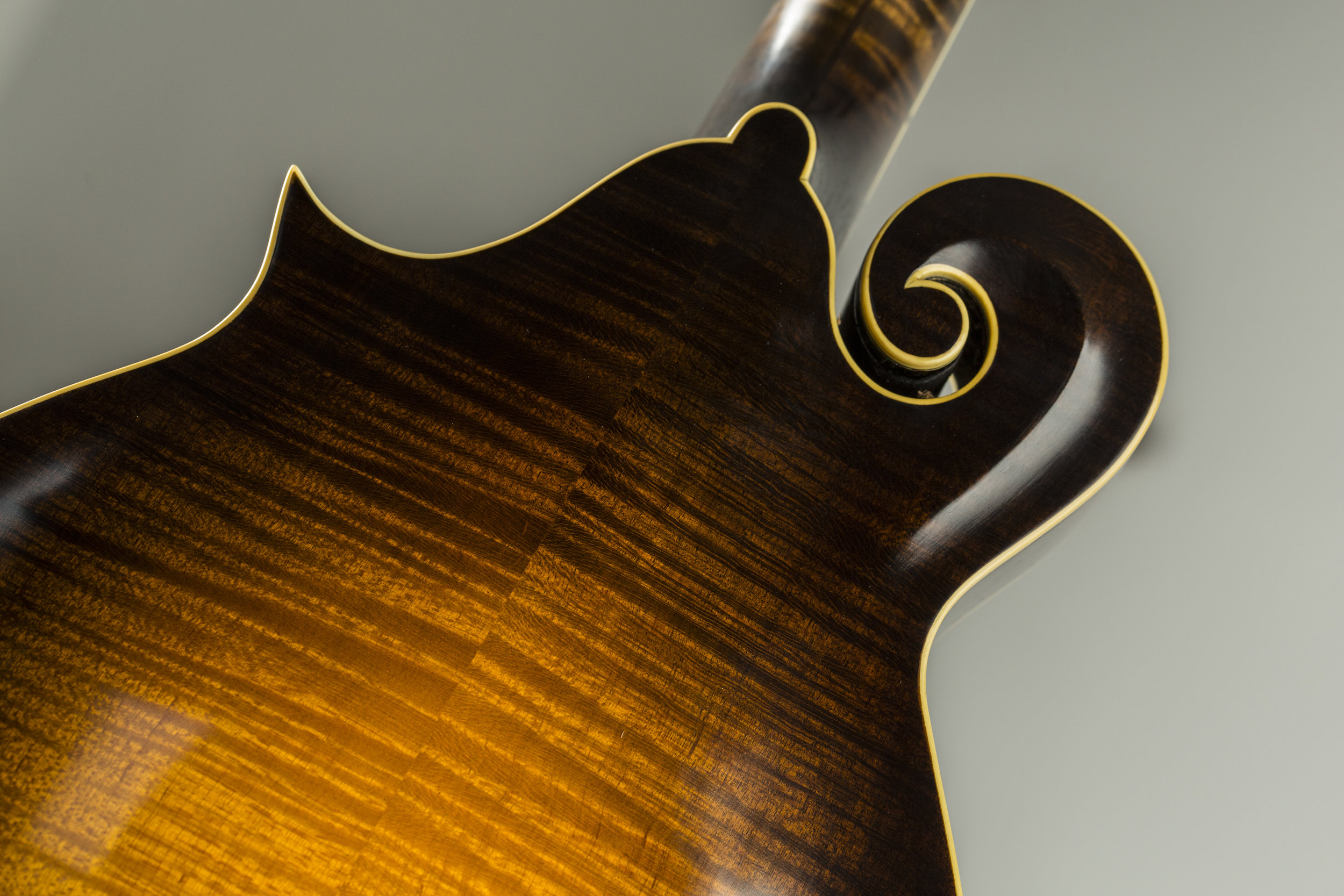
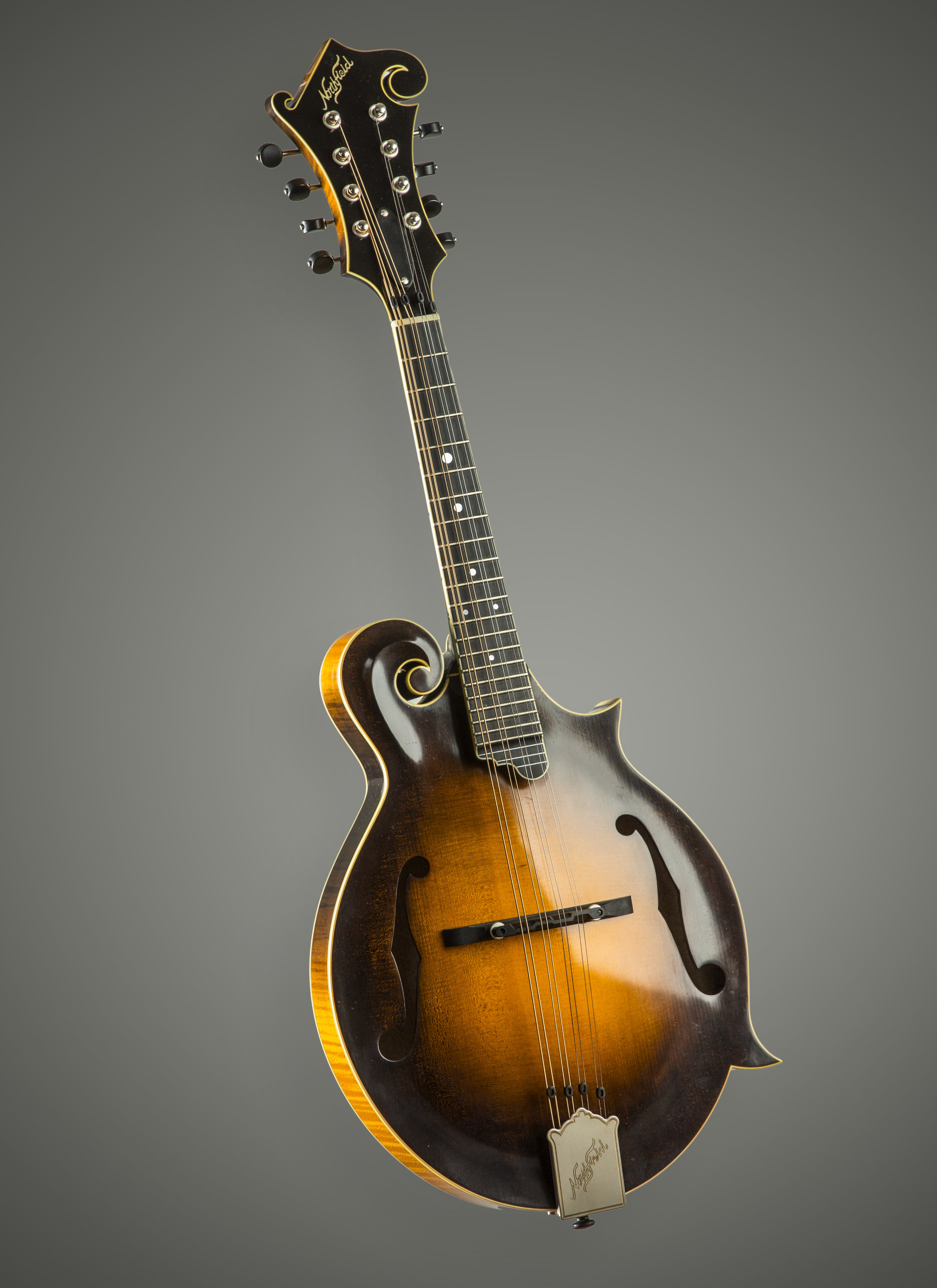
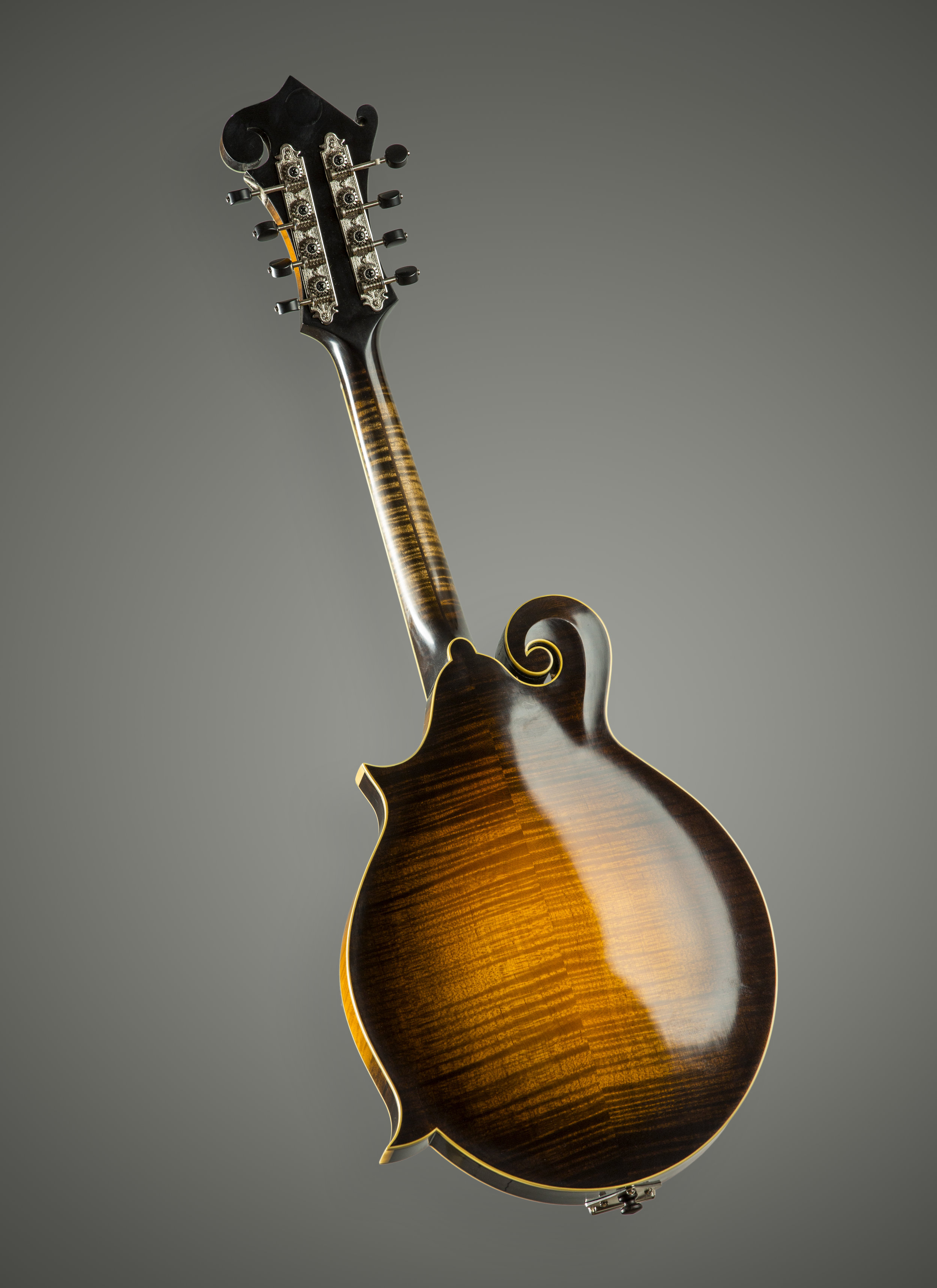
Northfield 4th
Generation F5
A diffuse light permeates the workshop through the thickly frosted windows. Coffee’s on. We find ourselves musing abstractly on our latest F5 development. We’ve approached mandolin making from many angles. The sum changes a degree with every design tweak. Where are we going? Pressing forward while looking backward? Time for another cup… A concept gleaned from the field of physics resonates with our latest F5 design process: The relation between the 3rd and 4th dimensions. Space and time – form and history.
The name: We call it this because it’s really the 4th time, in our more than ten-year history that we’ve revamped our approach to the F5. New directions, new motives, new design/dimensions/fixtures/materials yield a new sound. Or is it an old sound? Everything is about interpretation. We think every mandolin player and maker is drawing from specific examples (or experiences) they have come across. As time goes by and the years start to accumulate you draw from a bigger well of information. For us it’s been about finding the links between the sounds we like, and the instruments we want to play. Again, the experience. This is now the 3rd variation in our Artist Series mandolin family - and it's quite different from the other two.
The inspiration: We’ve been incredibly privileged to work with world-class artists like Mike Marshall and get helpful and informed feedback (even buy precious instruments) from some of the best mandolin builders on earth. Of course, even those instruments, by those legendary builders, are interpretations of the old Kalamazoo made F5s. It’s kind of like the telephone game - they said/did this (pass along), they said/did this (pass along)... on and on. And the story changes. The context and the application for how you use that information (regardless of whether or not it’s still in its original form) is what ends up being important - even when, or we could say especially when, the end results weren't anticipated. Like the original F5s being designed for classical music and orchestral ensembles and then, after some on-the-job experimenting, they become the standard for Bluegrass music. This yielded a new horizon for the mandolin. So, we go experimenting with bluegrass and mandolin designs only to come back around, deep in classical and other music. We ultimately deciphered for ourselves why the original F5 designs work in those varied contexts - AND why certain aspects to the design really are critical in a performance setting.
Specs
Price From $7995
Top: Adirondack Red Spruce
Back / Neck / Sides: Highly Figured Maple
Bridge / Fingerboard: Ebony
Tuners: Gotoh Deluxe Tuners
Tailpiece: Nickel-plated engraved Gilchrist/Northfield
Binding: Side or Top Triple-Bound
Pick Guard: Bound Celluloid Tortoise
Nut Width: 1-1/8" (28mm)
Fingerboard Radius: 5.7" at nut, 7.7" at 20th fret
Custom Options
Nut Width: Wide Nut 1 & 3/16" - “Adam Steffey” 1 & 1/4”
Head Stock Inlay:
Scroll Work Inlay - NC
Torch Inlay - NC
Deluxe Inlay - $500
"Artist Inlay" - $500Tailpiece: Nugget Tailpiece
Finish: Hybrid Varnish
Color: Hand-worked Antique Sunburst
Strings: Northfield Medium Phosphor Bronze
Case: Airloom “Recurve”
Origin: After a lot of experimentation we have decided to make this instrument collaboratively between our two workshops. It's one part practicality and one part continuity. In our efforts to build the amount of instruments we feel there is demand for we need to enlist all of our experienced staff to share the extensive load of work involved in F5 production. There is CNC operation, assembly, binding, long hours of sanding, etc. Like a great musical band we have a sense of place, cooperation, and overlap between many tasks. The delicate art of shading and finishing is an enormous consideration. Our long-time team member Lao Yin is a master of the coloring and finishing of musical instruments. It would be folly for us not to entrust him with the task of shading and bursting our premier mandolins. We believe it’s the hands, eyes, and experience that make the mandolin. Here's our process: All wood selection is done from our Michigan shop’s premium stash. We make all of the mandolin parts in Michigan, utilizing machines, fixtures, and handwork. With the top and back carved, ribs formed, blocks set, and neck completed with truss rod, overlays, and fretboard we partially assemble the instrument. The top and rib assembly are glued up, the dovetail neck joint is fine-tuned and fit to the body. The neck is then removed so we can pack the instrument "kit" in a box along with other supplies we're sending to the gang in Qingdao. The assembly is completed and then sanding and coloring steps are performed by Lao Yin. After a couple weeks of curing the mandolin is sent back to us in Michigan where we then perform final finish steps, wet sanding, french polishing, hardware installation, and setup. Sound difficult? It is - but that's how we'll do it. Together. That's how we've done everything and that's why we're confident we're making better instruments than we ever have.
Our reason: Why go back and change again? We wanted a specific voicing. We wanted the toughness and clarity in projection, within a band context. We’d heard this perfected by a handful of instruments: a 1922 F5, an amazing reproduction of that instrument made by Mike Kemnitzer that I acquired a couple years ago, Mike Marshall’s F5, and one of our own Artist Series mandolins. We borrowed, we modified, we built examples and we recorded extensively in a variety of settings. We prepared instruments for Mike Marshall's on-the-job experimenting (and thrashing…we love you Mike) and he took it to them, hard. After every instrument we'd gather comments, make some tweaks and hold our breath. After a couple years of testing we know we have something different and worth reporting on.
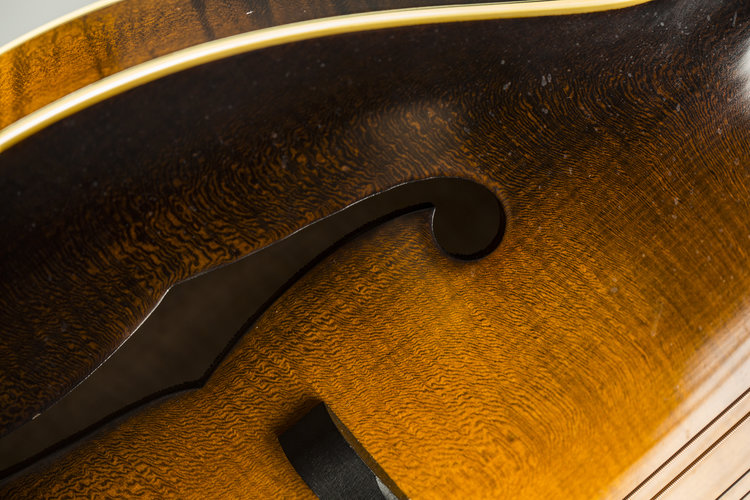
The result: A more robustly built instrument, with a distinct mid range and strong high-end voicing. A quick-to-sound responsiveness along with the toughness (“bones” as Mike would say) needed to propel projection and carve out sonic space in an ensemble. These are all things we’ve been working on and talking about since we started the Artist Series mandolins and this is the closest we’ve gotten to defining this character. The balance between power and warmth. Lastly, our building process has matured alongside these other developments to continually guarantee consistent results.